1: After the mold is used for a long time, the cutting edge must be ground. After grinding, the cutting edge surface must be demagnetized, and it cannot be magnetic, otherwise it is easy to cause material blocking. Enterprises using molds should make detailed records and statistics of their use, care (lubrication, cleaning, rust prevention) and damage, so as to find out which parts and components have been damaged and the degree of wear, so as to provide information for finding and solving problems. As well as the molding process parameters of the mold and the materials used in the product, in order to shorten the trial run time of the mold and improve production efficiency. The various properties of the mold should be tested under the normal operation of the injection molding machine and the mold, and the dimensions of the final molded plastic parts should be measured. Through this information, the current state of the mold can be determined, and the cavity, core, cooling system and Where the parting surface is damaged, according to the information provided by the plastic part, the damage state of the mold and the maintenance measures can be judged.
2: Springs and other elastic parts are most easily damaged during use, and usually break and deform. The method to be adopted is replacement. During the replacement process, attention must be paid to the specifications and models of the springs. The specifications and models of the springs are confirmed by three items: color, outer diameter and length. Only when the three items are the same can they be replaced. The quality of imported springs is better.
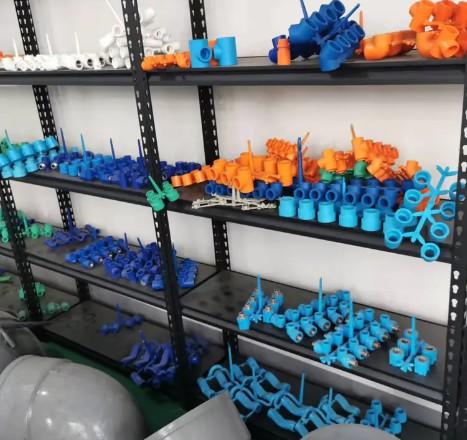
Commodity Mould
3: During the use of the mold, the punch is prone to breakage, bending and gnawing, and the punching sleeve is generally gnawed. Damaged punches and sleeves are generally replaced with parts of the same specification. The parameters of the punch mainly include the size of the working part, the size of the installation part, and the length.
4: Fasten the parts, check whether the fastening parts are loose or damaged, and the method to be adopted is to find parts of the same specification for replacement.
5: Pressing parts such as pressing plate, Youli glue, etc., unloading parts such as stripping plate, pneumatic ejector, etc. During maintenance, check the relationship between the parts of each part and whether there is damage, repair the damaged part, check whether there is air leakage by pneumatic jacking, and take measures for the specific situation. Replace air tube if damaged. It is necessary to focus on tracking and testing several important parts of the mold 6: The function of the ejector and guide parts is to ensure the opening and closing movement of the mold and the ejection of the plastic parts. If any part of it is stuck due to damage, it will cause production to stop. Keep the mold thimble and guide post lubricated (the most suitable lubricant should be selected), and regularly check whether the thimble, guide post, etc. are deformed and damaged on the surface. Once found, they should be replaced in time; The surface, movement, and guide parts are coated with professional anti-rust oil, and special attention should be paid to the protection of the elastic strength of gears, rack mold bearing parts and spring molds to ensure that they are always in the best working condition; with the production time Continuously, the cooling channel is easy to deposit scale, rust, silt and algae, etc., which makes the cross section of the cooling channel smaller and the cooling channel narrower, greatly reducing the heat exchange rate between the cooling liquid and the mold, and increasing the production cost of the enterprise. Cleaning should be paid attention to; for hot runner molds, the maintenance of heating and control systems is conducive to preventing production failures, so it is particularly important.