PE pipe fitting molds play a vital role in reducing the risks of leakage and ensuring the integrity of pipeline systems. The precise design and manufacturing of fittings through molds result in tight and secure connections between pipes. This eliminates the possibility of leakage, which is a critical concern in industries such as water supply, gas distribution, and chemical processing. The use of PE pipe fitting molds ensures that the fittings are properly aligned, tightly sealed, and resistant to pressure, maintaining the integrity of the pipeline system. By minimizing the risk of leakage, these molds contribute to the safety, efficiency, and longevity of pipeline installations, reducing the potential for environmental contamination, operational disruptions, and costly repairs.
the development of PE pipe fitting molds has led to advancements in design and functionality, offering a wide range of fittings to meet diverse industry requirements. Manufacturers have introduced innovative designs and configurations, including elbows, tees, reducers, couplings, and flanges, among others. These molds allow for the production of fittings with different angles, diameters, and connection methods, accommodating various pipeline layouts and specifications. The availability of a comprehensive range of fittings ensures flexibility and adaptability in pipeline design and installation, catering to the specific needs of different industries and applications. This versatility improves the overall efficiency and performance of pipeline systems, enabling seamless fluid or gas flow and facilitating system maintenance and repairs.
the use of PE pipe fitting molds contributes to the overall sustainability of pipeline systems. PE pipes are known for their durability, resistance to corrosion, and low maintenance requirements. The precise and reliable connections facilitated by these molds enhance the overall performance of PE pipelines, minimizing the risk of pipe failures and the associated environmental impacts. By reducing leakage, pipeline systems become more efficient, leading to improved energy conservation and reduced resource wastage. Furthermore, the recyclability of PE materials used in pipe fittings aligns with sustainable practices, reducing the environmental footprint associated with pipeline installations and replacements.
The development of PE pipe fitting molds has also driven innovation in the field of pipeline technology. Manufacturers are continually improving mold designs, incorporating features such as improved sealing mechanisms, enhanced durability, and compatibility with advanced joining techniques. This continuous innovation contributes to the evolution of pipeline systems, enabling the implementation of new technologies, materials, and construction methods. The advancements in PE pipe fitting molds foster a culture of innovation and improvement in the pipeline industry, driving progress in areas such as leak detection, pipe monitoring, and system optimization.
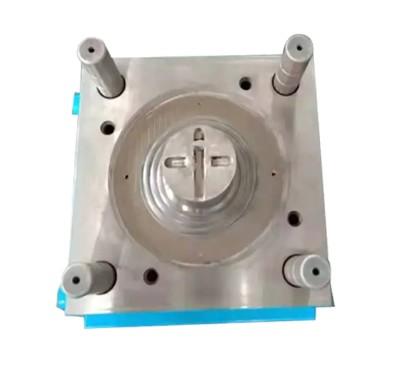