2. Cost Savings: By using daily necessities molds, manufacturers can achieve significant cost savings. The initial investment in molds may be higher, but the long-term benefits outweigh the costs. Molds are durable and can be used repeatedly, reducing the need for constant replacements. Moreover, the high production efficiency achieved through mold-based manufacturing helps minimize labor costs and material wastage.
3. Consistency and Quality Control: Daily necessities molds ensure consistent and uniform production of products. The molds are precision-engineered to create identical shapes and sizes with every production cycle. This standardized production process enhances quality control, reducing variations and defects in the final products. Manufacturers can deliver consistent, high-quality products to meet consumer demands and maintain a competitive edge in the market.
4. Design Flexibility: Daily necessities molds offer design flexibility, allowing manufacturers to create products with intricate shapes and patterns. With the advancement of mold-making technologies, complex designs can be accurately replicated, giving manufacturers the freedom to innovate and meet diverse consumer preferences. The ability to customize products efficiently through molds opens up new possibilities for product differentiation and market expansion.
5. Rapid Prototyping: Daily necessities molds play a pivotal role in the rapid prototyping process. Manufacturers can quickly create prototypes of new products using molds, allowing for faster testing and refinement of designs. This accelerates the product development cycle and enables manufacturers to bring new products to market swiftly, gaining a competitive advantage.
6. Scalability: Daily necessities molds provide scalability options for manufacturers. As demand for a particular product increases, molds can be replicated or modified to increase production capacity. Manufacturers can easily scale up their operations to meet market demand without significant disruptions or delays.
7. Sustainability: The use of daily necessities molds can contribute to sustainable manufacturing practices. By optimizing production efficiency, manufacturers can reduce material waste, energy consumption, and carbon emissions. Additionally, molds enable the use of recyclable and eco-friendly materials, aligning with environmental sustainability goals.
8. Industry Advancements: The ongoing advancements in mold-making technologies are further revolutionizing the manufacturing industry. Innovations such as 3D printing and computer-aided design (CAD) have enhanced the precision and complexity achievable in mold manufacturing. These advancements open up new possibilities for product design, material choices, and production efficiency.
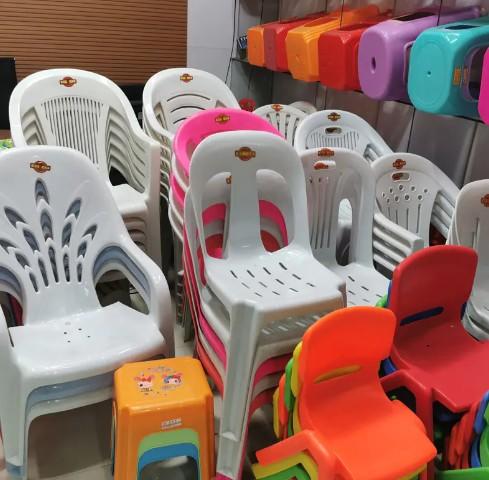